可溶性疏水性标签辅助的高效连续流液相多肽合成
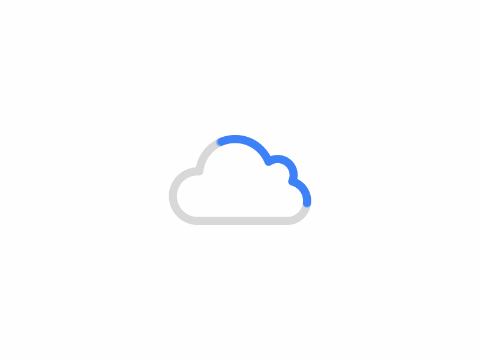
开发绿色、高效的合成工艺是实现治疗性多肽商业化生产的迫切要求. 报道了在微反应器中一种新型疏水性硅基载体双(4-((叔丁基二甲基硅基)氧基)苯基)甲胺(SPPM)辅助进行连续流动液相多肽合成(LPPS)的方法, 该方案由酰胺化模块(微通道反应器, 偶联时间 9.0 s)、脱保护模块(填充床反应器, 脱保护时间 31.4 s)和萃取洗涤模块(微通道混合器,洗涤 18.0 s)组成. 采用绿色溶剂(用乙酸乙酯代替被限制使用的 N,N-二甲基甲酰胺)和 N-苄氧羰基氨基酸(用氢解脱保护代替易制毒管制化学品哌啶脱保护), 合成了高纯度的(粗品收率>90%)五肽-3. 这种精确控制反应时间和温度的连续流方法, 从绿色和可持续的角度出发, 为大规模多肽合成开辟了新的前景.
关键词 连续流动; 微反应器; 可溶性载体; 液相多肽合成
治疗性多肽药物由于毒性小、副作用低、选择性高、半衰期短等优势已成为国际新药研究的热点[1], 拥有极大的市场需求, 国内外制药企业纷纷投入巨资来研发多肽药物, 因此开发合成多肽药物的方法尤为重要. 目前常见的化学合成方法主要有溶液合成法(CSPS)、固相合成法(SPPS)和液相合成法(LPPS)三种[2-4]. CSPS 的弊端在于连接几个氨基酸反应体系会出现不溶解的问题, 对于长链多肽药物的研究来说, 该方案是难以进行的[4-6].
固相合成法(SPPS)是 Merrifield[7]于 1963 年开发出来的多肽合成技术, 由于其操作简单、纯度高等特点,尤其微波辅助固相合成法成为目前最常用的合成多肽方法, 尹昊等[8]在微波固相多肽合成中运用偶联试剂N,N-二异丙基碳二亚胺(DIC)/Oxyma, 在高温下高效完成蝎子毒素多肽 Wa Tx 的化学合成及氧化折叠研究. 现今天然糖蛋白可通过多种化学方法合成及纯化获得, 在每个聚糖单元之间以及在聚糖链和蛋白质之间构建不同形式的糖苷键[9]. 彭鹏课题组[10]通过优化微波辅助固相多肽合成(SPPS)实现高效的糖肽组装. 然而, 固相合成是在非均相反应体系中进行, 反应过程难以监测和分析, 合成过程中还需要昂贵的树脂、过量的氨基酸、偶联试剂以及有害溶剂等, 原子经济性差且容易产生副反应, 会对环境造成不可逆的破坏[11], 因此人们一直追求和开发新的更快更绿色的合成多肽工艺.
相较于溶液合成和固相合成在原子经济性和绿色可持续性生产来说, 液相合成方法结合可溶性载体为肽链提供 C 端保护基团, 实现偶联和脱保护过程实时监测, 可控制偶联试剂和反应溶剂的用量, 在多肽合成方面更具潜力(Figure 1)[3c,12-13]. 1965 年, Shemyakin 课题组[14]利用非交联型聚苯乙烯(约 200000 分子量)通过氯甲基化制备一种可溶性聚合物载体, 能很好地溶解在N,N-二甲基甲酰胺或者二噁烷溶剂中与氨基酸进行偶联反应, 但由于聚合物自身溶解度和沉降析出而导致多肽产品纯度和产率很低. 此后, Bayer 和 Mutter[15]结合了CSPS 和 SPPS 的潜在优势, 使用可溶性聚合物(PEG)在溶液中进行反应, 基于 PEG 标签的 LPPS 将被称为PEG-LPPS[16], 但是这种聚合物载体负载能力较弱, 产率极低. 为应对大分子聚合物载体出现的问题, 国内外科研团队纷纷将目光投向小分子可溶性载体, 早在本世纪初, Hitoshi 课题组[17]报道了一种长链脂肪烃的苄醇衍生物载体,此外, Takahashi 小组[18]使用一种结构类似Fmoc 基团的氟衍生物(a1)作为疏水标签, 通过重复偶联和脱保护反应后配合水洗与沉降除杂来延长肽链. 随后, 该团队[19]又提出一种侧链为长链烷烃的二苯甲胺型载体分子(a2), 这种载体适应性强, 可以在 1-乙基-(3-二甲基氨基丙基)碳酰二亚胺盐酸盐(EDC•HCl)/1-羟基苯并三唑(HOBt)缩合体系中合成多肽, 并且能在三氟乙酸(TFA)的裂解液中很容易被脱除. 最近, 钦传光团队[20]在多肽合成纯化方面开发了含磷小分子载体作为氨基酸的 C 端保护基团, 这种载体在合成多肽之后可以回收并直接再利用, 提高多肽纯度和产率, 在有机合成和多肽合成领域具有突出的实际应用价值. 王萍团队[21]报道了一个在糖化学合成中利用液相载体的新发现: 在整个合成过程中可以进行简单快速的沉淀离心后处理,为合成复杂低聚糖提供一种高效、环保的方案.
另一方面, 连续流动合成技术在合成多肽方法领域取得巨大进展[22-26]. 微通道连续流合成的特点在于可以使用高活性但结构不太稳定的化学物质或高温条件来加速多肽的合成, 尤其结合了近年来热门的微流动技术、自动合成和在线监测技术, 不仅提高了合成的效率,而且可以将合成过程变得“自动化”和“可视化”[27-32].
近年来越来越多的关注点聚焦在多肽绿色合成的新技术、新工艺及新设备上. Kappe 课题组[33]报道了一种快速固相合成结合肽键的过程. Mijalis 课题组[34]开发了一种可以在自动化控制每隔 1.8 min 或在手动操作每隔 3 min 接入一个氨基酸残基的技术. Pentelute 课题组[35]研发了一种连续流动 SPPS 的自动快速多肽合成方法(AFPS), 可用于制备一条多达 164 个氨基酸的长肽,在90 ℃下使用20~100 equiv.的过量试剂, 只需要40~120 s 就可以完成一个合成周期. Mandity 团队[36]开发了一种用于合成多肽的高效连续流技术, 该方法在偶联过程中需要 1.5 equiv.的氨基酸, 同时产生定量的转化, 并且设计了一个高温、高压的合成反应器, 但在固相合成过程中仍避免不了使用昂贵的树脂、易制毒化学品哌啶以及大量的溶剂, 不仅耗费大量资源还严重污染生态环境[37], 因此连续流技术在液相合成中的应用将更具优势. Fuse 课题组[38]采用注射泵在 T 型混合器中连续流动合成多肽, 近期, Fuse 课题组[39]还开发了一个连续流动液相多肽合成仪用来自动合成制备 C 端游离肽. 李士杰等[40]利用在微通道反应器传质传热效率高的优点, 探究在微通道反应器中反应温度、反应液浓度以及停留时间对偶联反应的影响, 优化流动反应条件, 实现更加高效合成亮丙瑞林, 为液相多肽连续化合成技术提供借鉴和参考.
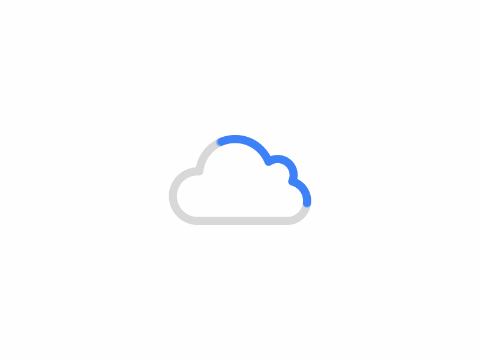
针对现有多肽合成技术的瓶颈与痛点, 目前亟需的是开发连续绿色多肽合成新方法. 本文提出一种具有自主知识产权的全新分子结构C端疏水载体SPPM替代树脂与前沿化工技术(微通道反应器、固定床流动反应器等)相结合, 优化反应条件, 原料试剂及溶剂消耗量大幅减少, 生产监测高度可控, 从而更加高效地合成多肽.
1 结果与讨论
1.1 可溶性载体合成
1.1.1 可溶性载体的合成步骤
可溶性硅基载体 SPPM 的合成路线如 Scheme 1 所示.
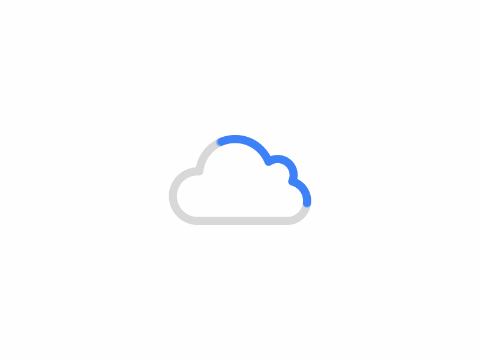
1.1.2 可溶性载体的优势
本文设计合成的是一种二苯甲胺型载体, 支链是叔丁基二甲基硅烷结构, 合成原料易得, 成本低廉, 过程简单, 并具有很强的疏水性, 在有机溶剂中的溶解性强,对酸碱环境都能耐受, 作为多肽 C 端的保护基, 实现实时监测反应, 用于 EDC•HCl/HOBt 缩合体系中合成酰胺肽类药物.
1.2 反应装置的构建
反应装置主要由三个部分组成: 连续偶联装置、连续流动加氢装置、萃取洗涤装置三个模块. 偶联和洗涤模块都是由微通道反应器、高压恒流泵组成; 流动加氢模块由 316 L 不锈钢材质管路、高压恒流泵、钯碳填充柱(柱管规格为 100 mm×10 mm, 柱内填充 Pd/C 催化剂)和氢气钢瓶组成. 图 2 是其结构示意图: Cbz 保护的氨基酸、EDC•HCl、HOBt 充分溶解在溶剂中作为溶液A, 可溶性硅基载体 SPPM 溶于溶剂中作为溶液 B, 溶液 A 和溶液 B同时以相同流速泵入微通道反应器. 反应结束后, 在微通道反应器内, 同时分别通入等体积等流速的反应液和 50 g/L K2CO3溶液进行洗涤单元操作, 结束后将收集液分液, 取上层有机相, 再将有机相与氢气混合, 泵入到钯碳填充床反应器中, 催化氢解脱除苄氧羰基, 不断重复偶联-洗涤-脱保护-洗涤过程, 即可完成全保护肽链的合成.
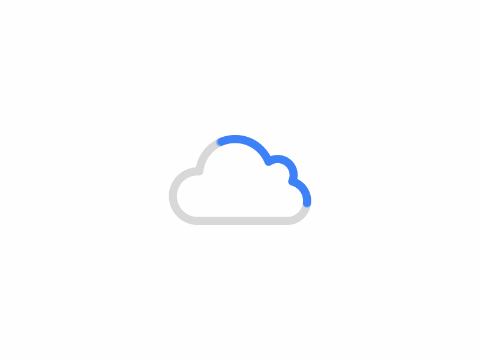
1.3 反应溶剂的选择
以可溶性载体 SPPM 和 N-苄氧羰基保护的丙氨酸(Cbz-Ala-OH)为模板反应, 连续流动偶联合成 Cbz-Ala�SPPM (1). 首先将 Cbz-Ala-OH 和偶联试剂 EDC•HCl、HOBt 溶于乙酸乙酯(EA)、四氢呋喃(THF)和二氯甲烷(DCM)三种溶剂中作为溶液 A, 氨基酸浓度为 0.27mmol/mL, 将 SPPM 分别溶于 EA、THF、DCM 作为溶液 B, 载体浓度 0.24 mmol/mL. 使用图 3 所示装置, 在室温条件下选择不同溶剂对连续流偶联条件效果进行测试, 得到的转化率和收率结果见表 1. 当使用乙酸乙酯为反应溶剂, 反应转化率和收率远高于另外两种溶剂, 并且可以完全反应. 本文选择几种不同氨基酸进行连续流偶联效果测试, 验证乙酸乙酯是否对氨基酸偶联效果具有普适性, 结果如表 2, 其他几种氨基酸与载体在乙酸乙酯溶剂中偶联反应转化率和收率都很高.
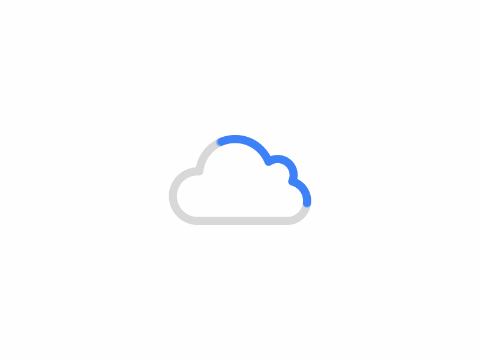
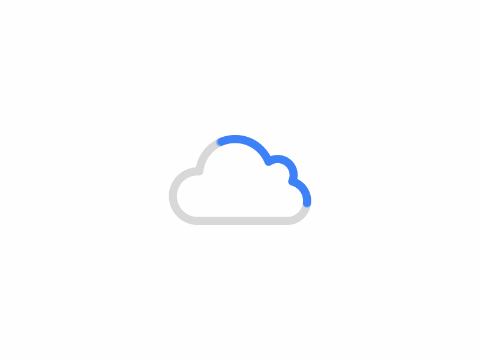
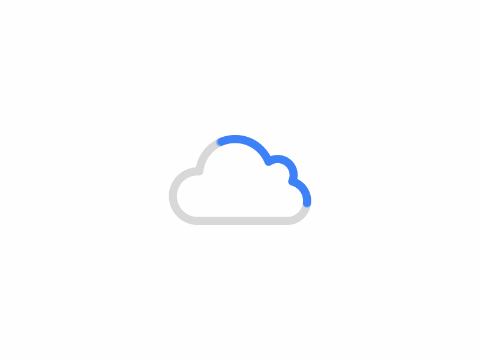
1.4 偶联反应条件的优化
偶联反应的转化率主要与微通道反应器的温度、流速以及反应液在微反应器内的保留时间有关. 以 Cbz�Ser(tBu)-OH 和 SPPM 的偶联缩合反应为模板反应, Cbz�Ser(tBu)-OH、EDC•HCl 和 HOBt 溶于乙酸乙酯中预先搅拌活化后作为溶液 A, 其中氨基酸浓度为 0.27 mmol/mL, SPPM 溶于乙酸乙酯作为溶液 B, 浓度为 0.24mmol/mL. 微通道反应器设备持液量为 3.0 mL, 改变流速后物料在反应器中的保留时间也会相应改变, 在控制温度不变条件下分别设置流速为 1.0、2.0、5.0、10.0、15.0 mL/min, 在控制流速不变的情况下设置反应温度为室温、30、40、50 ℃, 得到 Cbz-Ser(tBu)-SPPM (3)的转化率和产率如表 3 所示.
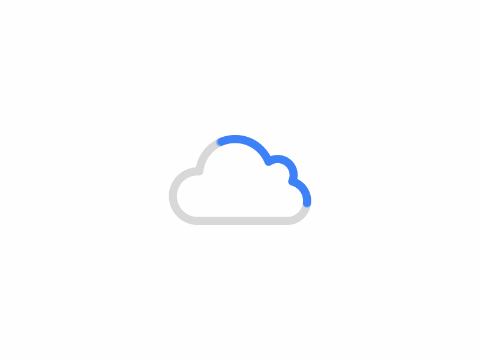
连续流动偶联反应的最佳条件是选择乙酸乙酯作为偶联反应溶剂, 微通道内温度为 30 ℃, 泵入流体的恒流泵流速为 10.0 mL/min, 偶联反应时间只需要 9.0 s就可以反应完全.
1.5 连续流动脱保护反应条件的优化
起初, 以传统脱保护方式尝试在反应瓶中进行催化加氢反应, 但如果完全脱除 Cbz 保护基需要数个小时的时间, 并且需要把钯碳催化剂过滤掉, 会造成物料损失,为缩短脱保护的时间, 提高反应转化率和收率, 搭建连续流动催化加氢装置. 为保证偶联和脱保护过程的连续性, 在脱保护过程中也使用乙酸乙酯作为溶剂, 在30 ℃条件下首先使化合物 Cbz-Ala-SPPM (1)与氢气混合, 经恒流泵注入到钯碳填充床反应器中, 脱除 Cbz 保护得到 H2N-Ala-SPPM (5), 并以此作为连续流脱保护探究实验的模板反应. 结果如表 4 所示, 在同流速(Entries1~4)泵入反应液的条件下, 氢气的压力越大, 产物的转化率越高, 当氢气压力达到 1.0 MPa 及以上时(Entries4~10), 泵入反应液的流速快慢不影响脱保护反应, 原因可能在于氢气压力足够大时, 填充床反应器内有充足氢气, 提供大量氢离子, 钯碳与反应液可以充分混合,脱保护过程效果比较好, Cbz 保护基可以被完全脱除.另外, 本文选择四种不同氨基酸[Cbz-Ala-SPPM (1),Cbz-Tyr(tBu)SPPM (2), Cbz-Ser(tBu)-SPPM (3), Cbz�Lys(Boc)-SPPM (4)]溶于乙酸乙酯中, 稳定氢气压力为1.5 MPa, 测试不同流速对脱保护反应的影响. 得到产物[H2N-Ala-SPPM (5), H2N-Tyr(tBu)-SPPM (6), H2N�Ser(tBu)SPPM (7), H2N-Lys(Boc)-SPPM (8)]的结果如表5 所示. 当钯碳填充床反应器内拥有充足氢气时, 四种不同 N-苄氧羰基保护的氨基酸在不同流速下, 转化率和收率没有太大差别, 因此反应液流速大小对脱保护反应没有什么影响, 反应液流速越大脱保护时间越短, 收率也很高.
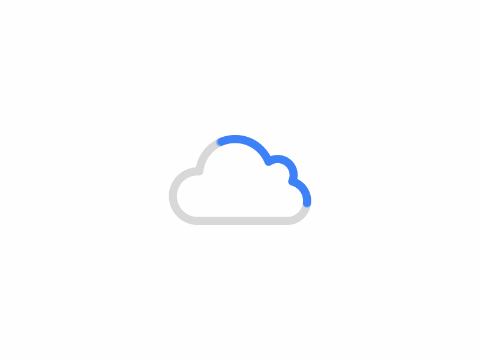
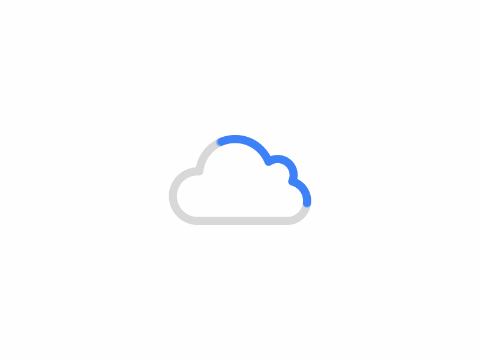
综上, 连续流动脱保护反应的最佳条件是: 选择乙酸乙酯作为脱保护反应溶剂, 填充床反应器内温度为30 ℃, 氢气压力为 1.5 MPa, 控制恒流泵流速为 15.0mL/min时, 脱保护反应的时间只需要31.4 s就可以完全反应, 反应的转化率和收率都很高.
1.6 微通道反应器中洗涤除杂效果
在该装置的工艺中, 洗涤模块是在偶联反应和脱保护反应后最重要的除杂过程. 为保证反应完全, 需要在偶联反应中投入过量的 N-苄氧羰基保护的氨基酸和偶联试剂 EDC•HCl、HOBt, 其中 EDC•HCl 和 HOBt 的水溶性都比较强, 洗涤除杂效果主要体现在洗去 N-苄氧羰基保护的氨基酸效率上. 本文测试了几个不同种类氨基酸在分液漏斗和微通道反应器内的洗涤效果, 其中微通道反应器洗涤条件是 50 g/L K2CO3 水溶液流速与反应液保持流速(5.0 mL/min)比分别为 1∶1, 1∶2, 使用分液漏斗洗涤条件为反应液与 50 g/L K2CO3 水溶液分别摇晃洗涤一次、两次、三次, 洗涤后静置分液(其中, 洗涤 H2N-Arg(Pbf)-OH 需要将 50 g/L K2CO3溶液换成体积分数为 3%的盐酸水溶液), 分别测试在有机相中残留的氨基酸量, 结果见表 6.
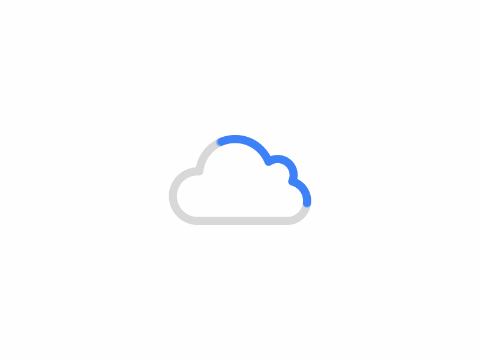
从表 6 结果可以看出, 微通道反应器中的洗涤效果要明显优于分液漏斗的洗涤效果, 并且大部分 N-苄氧羰基保护的氨基酸(Entries 1~5)在微通道内用等量等流速的碱水就可以被洗除, 比在分液漏斗中摇晃洗涤两至三遍才可完全洗干净更加简单便捷, 在洗涤液用量上也避免浪费, 有些 N-苄氧羰基保护的氨基酸(Entry 6)很难被洗净, 但是脱除苄氧羰基之后裸露氨基的氨基酸都是极易溶于水的, 无论是分液漏斗水洗还是微通道洗涤的效果都很好, 而且苄氧羰基脱除后体系特别干净, 副产物只有甲苯, 几乎没有清洗难度.
1.7 五肽-3 的合成
1.7.1 连续流动化合成五肽-3
五肽-3 的肽序为 H-Gly-Pro-Arg-Pro-Ala-CONH2,使用载体 SPPM 在连续流动装置中合成五肽-3, 其中所需的氨基酸均为市售的 Cbz 保护基氨基酸, 具体的操作步骤如 Scheme 2 所示.
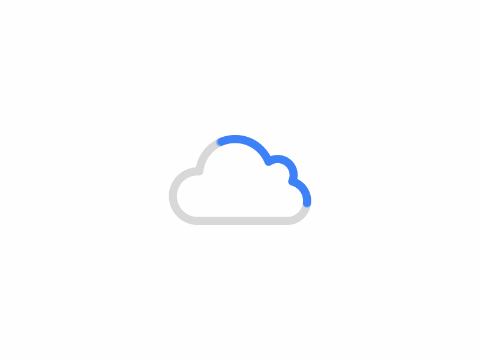
1.7.2 固相与连续流液相合成五肽-3 对比
(1) 合成时间、纯度和收率对比五肽-3 的固相合成方法是使用 Rink 树脂在固相反应器中运用鼓泡的方式完成偶联脱保护的过程, 使用N,N-二甲基甲酰胺(DMF)作溶剂, 体积分数为 20%的哌啶(溶于 DMF)脱保护, 一般完成一次完整的偶联-洗涤-脱保护-洗涤时间是 1.5 h, 而使用连续流液相合成技术在微通道中进行偶联反应和洗涤过程, 用乙酸乙酯作溶剂, 钯碳柱作脱保护单元, 完成一次完整偶联-洗涤-脱保护-洗涤时间只需要20 min, 结果如表 7 所示, 所得到产物纯度和收率都得到提高.
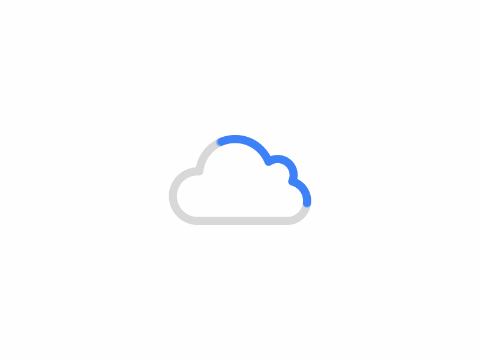
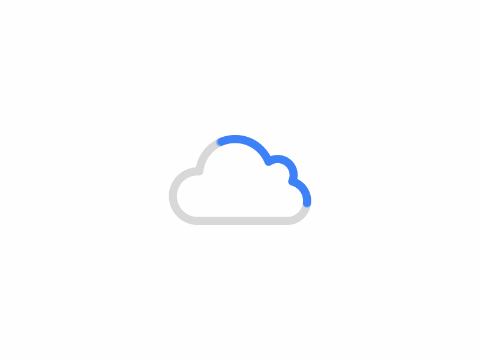
(2) PMI 对比
PMI 是指过程质量强度[41], 是整个反应过程中投入的物料总质量(包括溶剂和洗涤溶液)和目标产物质量的比值, 是衡量一个反应的关键指标, 当今在化工制药行业都在使用PMI作为评估原子利用率的一个指标. 在合成过程中投料一致的情况下, PMI 越低得到的产物越多,产生的废物就越少, 原子经济性更高. 以使用 5.0 mmolRink 树脂投料固相合成和 5.0 mmol 载体连续流动液相合成五肽-3 分别计算出各自的 PMI. 结果如表 8 所示,连续流液相合成的 PMI 指数远比固相合成指数低的多.
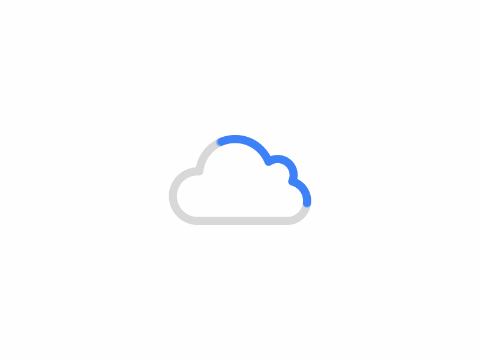
(3) 成本核算对比
如下表 9 所列出, 分别使用固相合成和连续流液相合成方式合成五肽-3 所需要的试剂成本对比.
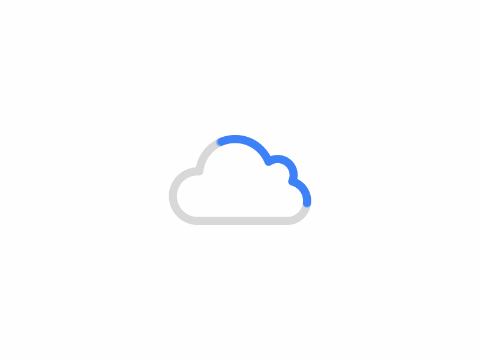
固相多肽合成反应为了保证合成效率, 每次偶联都需要投入 2 equiv.以上的氨基酸和偶联试剂, 还需要大量的溶剂反复洗涤树脂, 以保证多余偶联试剂和脱保护试剂被冲洗干净, 通常完成一次偶联和脱保护过程, 至少需要洗涤 10 遍树脂, 因此对洗涤溶剂的需求量特别大, 而连续流液相合成的洗涤部分采用碱水萃取除杂,这直接降低了合成成本. 连续流动液相合成方法使用Cbz 保护氨基酸, 相对于固相合成所用的 Fmoc 保护氨基酸价格也更加便宜, 均相反应原子经济性高, 减少试剂的用量和有机溶剂的消耗量, 乙酸乙酯也远比固相合成所用的 N,N-二甲基甲酰胺更加低毒绿色, 便宜安全.
(4) 固液相合成方法对比
如表10所示, 液相合成工艺灵活高效, 本文结合可溶性载体结构具有一定疏水性且在有机溶剂中有良好的溶解性, 使其可以在有机溶剂中依次完成偶联和脱保护过程, 通过碱水萃取洗涤除去氨基酸和偶联试剂等杂质, 完成多肽的全液相合成.
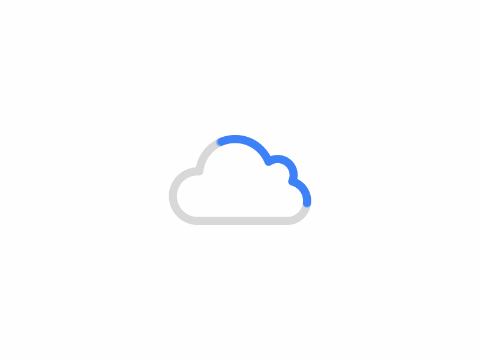
2 结论
介绍了一种新型硅基疏水标签 SPPM, 作为肽 C 端形成酰胺键的保护基团, 标签结构稳定, 既可以增强疏水性, 又可以实时监测反应进度, 将连续流动技术与多肽液相合成方法相结合实现更加高效、绿色地进行氨基酸的偶联与脱保护过程, 为液相多肽合成提供一个新的思路. 通过进一步优化连续流偶联和脱保护反应条件,使得偶联反应仅需要 9.0 s, 脱除保护反应需要 31.4 s,后处理水洗过程需要 18.0 s, 极大地提高了多肽合成的效率, 为实现大规模多肽药物的绿色合成奠定了基础.
免责声明:本文为行业交流学习,版权归 原作者所有,如有侵权,可联系删除。
共有 0 条评论